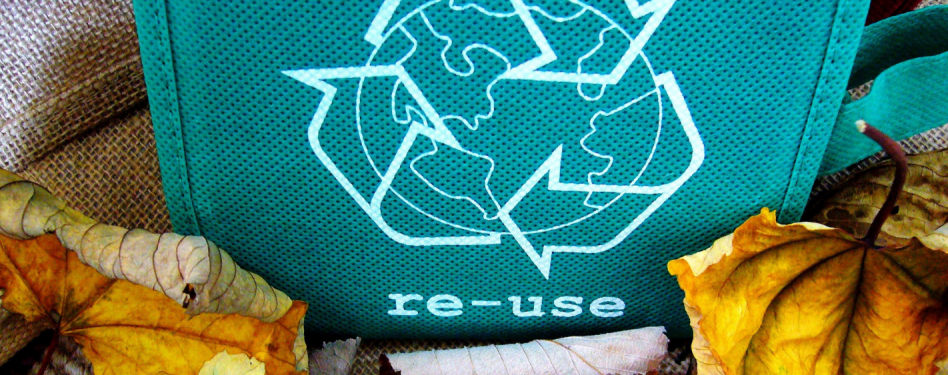
Continuing with the cost-savings strategies in TRUE, the next topic of our series is our third credit category in the TRUE Rating System– Reuse. You can find the rest of the articles in this cost-saving series on our website under the article section!
The goal of TRUE certification is to divert all solid waste from landfills, incineration (WTE), and the environment. There are many economic advantages embedded in the strategies of the TRUE rating system that help businesses cut costs and generate revenue.
One of the benefits of TRUE certification is the expedited return on investment (ROI). Compared to major investments into sustainability infrastructure, zero waste initiatives have remarkably low payback periods. Here are some of the top cost-saving or revenue-generating strategies within the Reuse credits of the rating system which illustrate the potential ROI for facilities pursuing TRUE.
Reuse
These TRUE credits focus on increasing reusability in production, packaging, shipping, and distribution as well as food service. By reusing, ongoing purchasing of single-use items, hauling and waste management costs are now avoided.
Credit 1: Develop systems that emphasize reuse
An example of a systems that emphasize reuse are donation programs and policies. Donations are a good practice that enables the reuse of materials through third parties, keeps valuable materials within a community and can possibly provide a tax benefit. Last year alone, more than 79 million Goodwill donors in the U.S. and Canada helped divert more than 2.5 billion pounds of usable goods from the waste stream.
This model is not just good for the planet, but for people as well. Goodwill uses the revenue from the sale of donated items to fund customized job training, employment placement and community-based services to people with disabilities, those who lack education or job experience, and others who face challenges finding employment.
There is also opportunity for donation when your facility is going through a renovation. Well-planned deconstruction can keep valuable building materials in their useful life and help others in the community.
Credit 2: Document pallet and shipping container reuse
Pallets, shipping containers, and shipping materials hold a lot of material value. Paired with reuse programs, these materials can often yield high returns for the company.
-
Straus Family Creamery has implemented reusable pallet wraps to replace single-use shrink wrap. Also, they use 75 reusable pallet wraps to transport products between facilities and in local distribution. These pallet wraps avoid about 15,000 pounds of waste annually while also reducing costs for the creamery.
-
Ductmate Industries returned over 2,000 pallets, saving 65 tons of lumber and $13,000 in the process.
Credit 3: Implement reusable transport containers
Reusable and sustainable transport containers promote a circular economy and reduce operational waste throughout the supply chain
-
Imagine saving $1 billion dollars and 2.7 billion trees through one simple action! By switching from a recycling program to a returnable container program for shipping materials, Toyota saved over 220 million pounds of wood and 145 million pounds of cardboard. What’s more, this program has saved them over $1 billion in packaging costs.
-
Kroger and Polymer logistics implemented Cleanpal, a more efficient and reusable pallet for maximized shipping space and easier storage.
Credit 5: Use reusable/durable food service ware
Purchasing single-use materials for internal dining areas or events create ongoing costs and waste generation. Ellen MacArthur Foundation identified that converting only 20% of plastic containers to be reusable is a $10 billion industry opportunity.
-
Many TRUE certified facilities, from universities (Chou Hall at UC Berkeley) to farms (Lundberg Family Farms) to warehouses (Ecover), have instituted reusable food service ware. Ecover replaced single-use utensils with reusable silverware and ensured that food sourced for employee lunches is packaged sustainably. In each instance, these companies decreased single-use plastic and saved substantially on costs.
Unfortunately, many of the items that companies use daily are seen as disposable and replaceable in our current practices. However, when you take a step back and consider the value of these items, you might be surprised at how much a facility can save by implementing effective reuse plans. Reuse plans and strategies are one of the many tools that can be utilized for realizing your facility’s zero waste goals. TRUE offers a roadmap to implementing reuse strategies in the most efficient way possible. Your facility can reduce operational costs and reduce waste by starting to implement these credits as well as beginning the process of becoming a TRUE certified project. For more information, download the TRUE Rating System to get started.