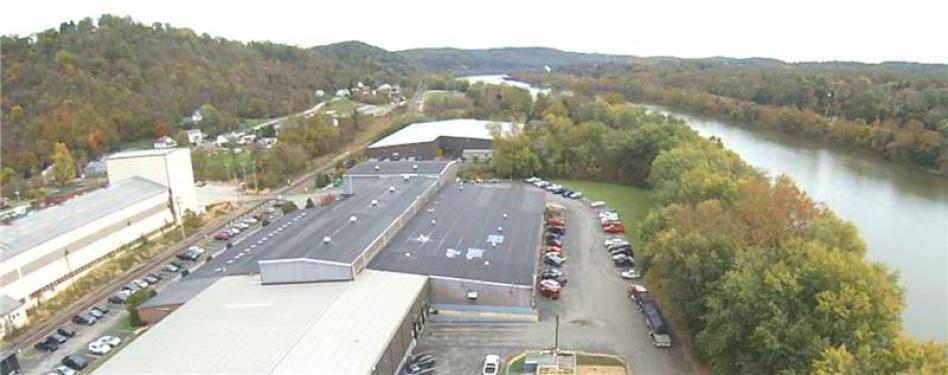
Sustainability is quickly becoming a universal expectation for industries of all kinds, but meeting ESG goals can be a challenge. While organizations can approach their sustainability goals through many different methods and targets, zero waste is quickly gaining popularity for manufacturing facilities in particular. As companies work towards their zero waste goals, it is important for them to verify their successes and to reaffirm their commitment to these goals. One of the ways this can be achieved is through TRUE certification, which offers a path to third-party verification while also providing the resources to work towards zero waste.
TRUE, or Total Resource Use and Efficiency, helps businesses and facilities improve their bottom line while reducing waste by focusing on upstream initiatives. The program is driven by a points-based rating system that is intended to provide a pathway to achieving the goal of zero waste. TRUE is particularly effective for driving change in the manufacturing sector, and facilities across multiple industries globally have used TRUE certification to achieve their zero waste goals.
The DMI Companies Monongahela Manufacturing Facility is one such example of highly effective zero waste policies. They achieved TRUE Silver certification for their 200,000 square foot facility in Monongahela, Pennsylvania in 2019, thanks to a 94.49% diversion rate. In 2020, they took their zero waste goals a step further and achieved TRUE Gold certification, diverting 96.65% of all waste from landfill and incineration. Now, they annually save an average of $45,000 in cost avoidance and over 11,000 MTCO2e of greenhouse gas (GHG) emissions through reduction, reuse and recycling.
In order to realign the facility workforce’s values toward zero waste, DMI Companies focused on employee training and cultivating a circular economy culture. Sustainability education now begins on day one with training during new employee on-boarding. Every new hire for this facility is taught the essentials of their zero waste goals and achievement methods. Further, a cross-departmental Sustainability Committee of employees was formed in 2021 to promote environmental stewardship strategies, making sure the facility stay clean and recycling stays uncontaminated. It allows for open discussion to keep growing DMI’s sustainability program.
To build connection between their zero waste goals and the unique aspects and materials of each department, DMI Companies began running “Dumpster Dives.” Employees examine what materials were thrown away and brainstorm ways to reduce the amount sent to landfills. Through their attention and focus on each department of the facility, DMI Companies demonstrates that understanding how your company operates is vital to achieving zero waste goals.
Their operations are based on the “Three Rs” – reduce, reuse, and recycle. DMI places emphasis on utilizing green purchasing and engineering strategies as a means to reduce and reuse. Reducing what they use and create in turn reduces the amount of waste generated.
In 2020, DMI’s Procurement team received training on the EPA’s Preferred Purchasing Strategy. DMI’s buyers are often challenged to buy locally sourced products where possible, and work with vendors to either reduce incoming packaging or completely redesign their packaging methods. One such example is a recent change made to the packaging of one of their raw materials, which originally was individually packaged in small plastic bags, combined into a larger plastic bag, placed into a cardboard box, and shrink wrapped. The vendor, after learning about DMI’s sustainability commitment, now packages this material loose in specially designed wooden crates. Thanks to their new shape, these crates are reused to ship customer orders. With this change, as well as the other environmentally preferred purchases, DMI Companies has saved thousands in procurement.
DMI Companies’ TRUE certification has also allowed them to become a leader in their community. As a member of several regional sustainability groups such as Sustainable Pittsburgh, the Green Building Alliance (GBA), and the Keystone Energy Efficiency Alliance (KEEA), DMI is able to help other businesses achieve their own sustainability visions. In the words of DMI Companies CEO/President Ray Yeager, “TRUE certification provided our organization with a means to quantify and recognize the amazing efforts of employees toward achievement of this goal.”
Building product manufacturers like DMI Companies are ideal candidates for TRUE certification and zero waste since material manufacturing processes are often resource intensive. This is why a key focus of the TRUE Rating System is Upstream Management. Building product manufacturers are the upstream vendors for building construction and operations. When a building products manufacturer reduces manufacturing waste and works toward circularity, they improve the environmental performance of every building that uses their products.
To encourage the use of circular building products, there is a Circular Products LEED Pilot Credit which rewards buildings that:
-
Use products manufactured in a zero waste setting;
-
are designed to be cycled multiple times through repair or remanufacturing, and
-
are recovered at the end of their useful life to be remade into new products.
“Building products have always been core to defining sustainable materials in LEED,” notes Wes Sullens, Director of Materials and Resources at the U.S. Green Building Council. “New credits in LEED like the Circular Products pilot credit reward strategies that foster sustainability in the manufacturing supply chain. By achieving TRUE certification, DMI Companies are leading the building products industry towards capturing the full value of materials and enabling a circular economy with zero waste.”
It is no secret that manufacturing is a waste-intensive industry. For every unit of waste we see in individual materials, 70 times that amount is generated during that material’s production. However, DMI Companies Monongahela Manufacturing Facility illustrates that zero waste is no longer just a dream — it is an operational practice and organizational mindset. In fact, zero waste can become such a cultural movement in a company that it spreads throughout all employees and locations. DMI Companies is working to expand its sustainable operations to its newest 200,000 square foot facility in Wagoner, Oklahoma.
No matter the industry, waste exists. However, with persistence and commitment, zero waste is not only achievable, but will also save you money, engage your employees and help you meet sustainability goals.